Published in the November 2000 Issue of Anvil Magazine
In 1993 Cooper Industries bought Diamond Tool from the Triangle
Corporation. In 1994 the forge operation and manufacture of horseshoes was
relocated to its forge facility in Monroe, North Carolina. There the Diamond
product line joined the forge operations of Cooper brands such as Crescent,
Wiss, H.K. Porter and Plumb. This facility is the largest forge, stamping
and investment cast operation in the country. It employs several types of
forging methods and the latest stamping processes, along with a state of
the art investment casting operation. The plant consumes 20 million pounds
of steel, producing over 30 million forgings and castings annually. The facility
manufactures over four million horseshoes a year.
Diamond Tool and Horseshoe Company was founded by Otto Swanstrom in 1908
and was known as the Diamond Calk Horseshoe Company. Otto, who was working
as a blacksmith in the lumber camps, realized that the time-consuming tasks
of shoe removal and sharpening of the calk could be improved. At that point
Otto invented the removable calk. The company began with two employees
manufacturing the patented calk for horseshoes. In 1912 Otto build his first
plant and began to manufacture horseshoes. Over the years the Diamond product
line expanded to include a full line of farrier tools as well as many other
hand tools and hand tool products. (See ANVIL Magazine interview with
CooperTool's Herb Buecher, August 1994.) |
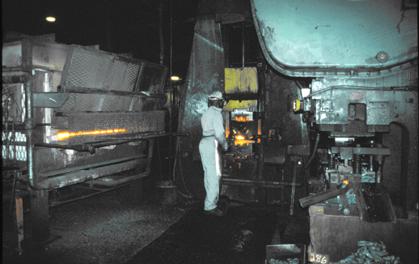 |
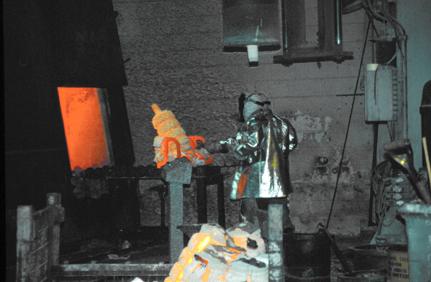 |
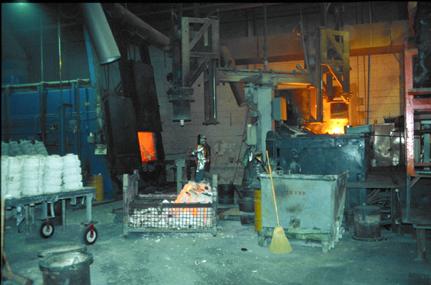 |
The horseshoe production process begins with the in-house
manufacturing of the required tooling. The dies used in the manufacture of
Diamond horseshoes are made on a state-of-the-art high-speed milling machine
that will produce the same shoe every time a new die is required. |
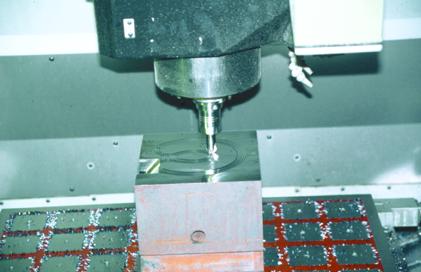 |
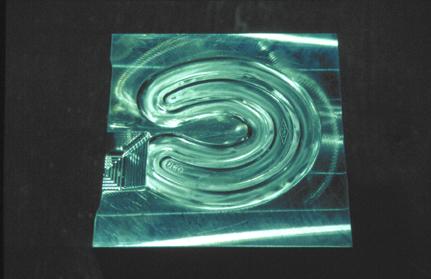 |
Steel is purchased from several certified steel vendors. The round bars
are then cut to the proper length for each product.
Bars are heated to 2200 degrees and then pre-formed into a horseshoe shape
before forging. |
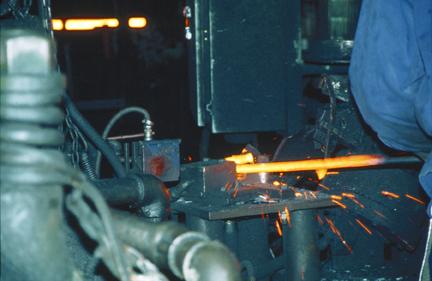 |
The shoes continue down the cell and are packed into quarter-keg boxes. Color-
coded labels are added, identifying the style of shoe and the date of its
manufacture.
The Diamond Horseshoes are transferred to the CooperTools distribution center
in Apex, North Carolina, where they are available for worldwide shipment
with other CooperTools family of products.
Return to the November 2000 Table of Contents
Return to the Farrier Articles Page
|